The Only Guide to Machine Nozzles
Spray nozzles are utilized to get rid of pollutants as well as are crucial in the cleansing process of lots of making processes. Kadant produces countless spray nozzles consisting of jet, follower, brush shower, disc fan, self-purging, trim squirt, and also quick link nozzles. Unique tipped nozzles such as ruby as well as cermet are likewise offered.
A clean melt, free of international particles is required for the hassle-free as well as cost-effective production of moulded components. Nearly all thermoplastics can be refined with the FN type filter nozzle. Just PVC is not ideal. By altering the melt flow this nozzle has an added benefit of a mixing impact which can enhance homogenization.
The common Herzog thaw filter is based on a perforated display as this style has much less pressure decline compared to various other filter kinds. This filter type appropriates for filtering bits larger than 0.6 mm. The second choice is based upon a void filter layout which is used for filtering particles smaller sized than 0.6 mm.
Any kind of foreign bits which are larger than the openings or gaps are kept back in the overview air duct. The filtered thaw circulations on via an outlet duct to the shot mould. Benefits of the filter nozzle type FN: • Aids decrease deny prices as a result of impure thaw • Stops mould as well as gate obstructions as a result of international bodies in the melt • Helps protect the mould • Assists melt homogenization (mixing effect) Technical Documentation:Device filter nozzle type FN (display or gap filter).
The Of Machine Nozzles
In today's worldwide manufacturing atmosphere, molders are aiming to enhance their injection molding procedures in every means feasible - machine nozzles. Numerous kinds of device nozzles can assist achieve that objective. Machine nozzles today can give a selection of features, consisting of filtering system, mixing, as well as shut-off of thaw circulation. Decreasing the clogging of gateways and/or warm runner tips because of foreign product orcontamination in the thaw stream with nozzle filters can readily improve uptime while also decreasing damages to entrances and hot-runner suggestions.
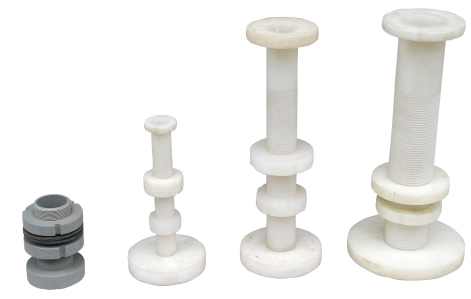
Lastly, shut-off nozzles can minimize drool in molding operations where journalism is often disengaged from the mold, such as in numerous two-shot molding applications. MODULAR NOZZLE DESIGNS Machine nozzles are designed to be quickly threaded onto the injection molding barrel. This suggests that the backside of each nozzle is customized to string onto the certain machine barrel for which it is to be used.
Some device nozzles are of single-piece construction, which may result in much less expenditure initially. Other nozzles are of modular layout as well as construction, which commonly uses different elements for the nozzle body, device interface, and also mold and mildew interface. Modular layouts supply a number benefits, the key one being the capability of a single nozzle body to interface with multiple injection barrels and multiple mold and mildews.
Separate user interfaces, each with the appropriate string requirements for the shot molding barrel that it is made use of on, can be connected to specific injection presses, each with a typical user interface to the nozzle body. In this way, the nozzle body might be after that be conveniently fitted to every one of the various shot molding barrels used in a molding facility.
Not known Details About Machine Nozzles
A modular maker nozzle layout consists of a modular suggestion that can be conveniently traded, enabling the molder to have multiple suggestions to enable one nozzle to correctly user interface with multiple molds, each with different sprue-bushing specs. SCREEN-PACK NOZZLE FILTERS Nozzle filterings system capture contaminants in the thaw stream to stop such particles from getting in the mold and also the molded components.


The most usual style is referred to as a screen pack (machine nozzles). It is composed of a metal disk perforated by a number of small openings, which is put along the inner diameter of the flow network of the equipment nozzle. As the thaw go through the flow channel of the nozzle, it runs into the metal disk and also is squeezed with the small-diameter openings.
Advantages of a screen pack are its straightforward style and also reduced expense. It is likewise fairly easy to size the sizes of the openings in the steel disk. There are several negative aspects to evaluate packs, also. The firstly drawback is that to guarantee the architectural honesty of the metal disk versus the shot molding pressure, the location of the strong steel will be more than the accumulated area of the small-diameter holes consisted of within the metal disk.
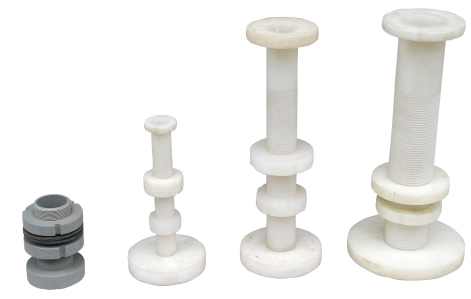
This leads to a noticeable as well as substantial stress drop as the melt traverses via the screen pack. This stress decline is huge sufficient to affect the processing window, and also thus is undesirable to several molders. Many molders will not use display packs or will restrict their use to shot molding presses and/or molds where this type of stress drop is deemed definitely essential.
About Machine Nozzles
As soon as a hole is obstructed the efficient circulation location of the melt is reduced even more, which causes an additional rise in the pressure decline. As more contaminants are caught, the pressure decrease proceeds to increase also further. Offered the fairly little efficient circulation location of the display pack to begin with, each further decrease in flow area has a visible additional rise in stress decline. machine nozzles.
At this point, the display pack must be cleansed, which reveals a third downside of this nozzle layout. To clean the display pack, the equipment nozzle must be cooled and also dismantled so that the screen pack can be removed from the nozzle filter. The display pack must after that be cleansed or changed.
As soon as reassembled, the device nozzle can then be brought back up to the proper operating temperature level and molding might recommence. The entire procedure from closure of molding, through cooling down, disassembly, cleaning, reassembly, and heating up, might conveniently take a number of hours or even more, depending upon the dimension of the device nozzle.
official source Get the facts imp source